MAN Energy Solutions offers its EGR system as an emissions solution for its new low-speed ME-GA engine
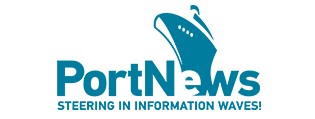
MAN Energy Solutions has announced that it is to offer its proprietary EGR (Exhaust Gas Recirculation) system as an emissions solution for its new, low-speed ME-GA engine, the Otto-cycle variant of its established ME-GI dual-fuel engine. EGR is a NOx-emissions-reduction technique that ensures IMO Tier III-compliance in both diesel and gas mode.
The company has long experience with the emission-reduction technology and reported the first order for an EGR system in 2011 when it was fully integrated within the MAN B&W 6S80ME-C9 main engine of a 4,500 teu containership newbuilding.
MAN Energy Solutions reports that EGR will enable the ME-GA to reduce specific gas consumption by ~3%, and specific fuel-oil consumption by 5%. It will also significantly reduce methane slip by 30 to 50% and solve the issue related to pre-ignition on Otto-cycle engines.
MAN Energy Solutions states that it has received orders for over 241 engines with EGR, with more than 33 units already in service. The company expects to deliver the first, commercial ME-GA low-pressure dual-fuel engine by end-2021.
As previously stated, EGR will help reduce the ME-GA’s methane slip by 30 to 50%, while lowering specific gas consumption by around 3% and specific fuel-oil consumption in diesel mode by 5%. EGR will enable the ME-GA to meet Tier III requirements in both fuel oil and gas modes without additional aftertreatment.
MAN Energy Solutions plans to make the EGR option available from late 2021, concurrent with the introduction of the ME-GA. The company’s experience with designing and delivering low-pressure and high-pressure EGR versions has enabled it to bring the new solution to market in a relatively short time.
The ME-GA EGR solution is a high-pressure system, which can be integrated into existing engine-room designs, and the EGR unit itself does not change the engine footprint. Its design-similarity to that of ME-C engines’ EGR systems will lower its price point, since the supply chain and components are already matured.
The EGR system works through drawing around 30 to 50% of the engine’s exhaust gas into the EGR receiver, where it passes through a pre spray to lower its temperature, before passing through a cooler spray. After passing through a water-mist catcher, the gas then goes through a blower to increase pressure back up to scavenging air pressure, before being fed back into the compressor and the engine.
The volume requirements of the ME-GA EGR system are significantly lower with, for example, less pipework required than for low-pressure EGR solutions.
Introducing an EGR solution also improves the stability of the combustion process. MAN Energy Solutions is currently researching how far it can lower methane slip while maintaining a good equilibrium with recirculation.
About ME-GA
MAN Energy Solutions is developing the high efficiency, low-pressure, two-stroke, dual-fuel MAN B&W ME-GA engine at its Research Centre Copenhagen. The engine delivers a low CAPEX solution aimed at certain vessel types and applications – such as LNG carriers – that are able to use ‘boil-off’ gas as a source of fuel, or smaller ships where low capital outlay is a priority.
Based on the well-proven MAN B&W dual-fuel design with minimal installation requirements, the MAN B&W ME-GA uses an efficient ignition concept and unique gas-admission system that delivers safe and reliable operation.
The ME-GA furthermore features minimal operational costs, simple supply and purging concepts, and low maintenance costs for its fuel-gas supply system.