WIND B.V. and TKF take wind power onshore
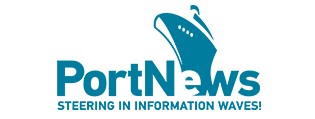
Every turbine in a wind farm has its own cables to transport offshore wind power ashore, and the miles and miles of cables required by the Fryslân wind farm are manufactured by TKF (Twentsche Kabelfabriek). WIND B.V., a company based in Alkmaar in North Holland province, is in charge of logistics.
The Amsterdam/IJmuiden region and Port of Amsterdam are pulling out all the stops for offshore wind power. To facilitate the construction of wind farms, we’re manufacturing and shipping various parts via the North Sea Canal Area. In a series of four interviews, we tell you about are stance on building offshore wind farms. Speaking this time: Tom Nooij, Managing Director of Wind B.V and Gert van den Hoek, Project Manager at TKF. Topic of conversation: cables – as far as the eye can see.
Exceptional cable quality
Gert van den Hoek: ‘Since subsea power cables are exposed to all sorts of stressors and environmental factors – including salt, moisture, corrosion and attrition – most manufacturers use bitumen. But while this is a very strong and durable adhesive, it’s not really sustainable. On top of that, it’s not very user-friendly for installation engineers – when stripping the stuff they’re covered head to toe with black gunk.’ When developing its Lochem-based production facility back in 2014, TKF therefore decided to start using all-new materials. ‘We picked materials that were easier to install, sustainable, and strong, as it’s not that easy to remove cables from the seafloor. So it was all a bit touch-and-go for a while there, but fortunately it all worked out really well.’
Storage and transport
As soon as the subsea cables roll off the conveyor belt at the Lochem site they require a temporary storage space, as it often takes many months before a wind farm actually needs them. This is where WIND B.V. comes in, which provides just such a storage facility. The cables are loaded onto a barge purpose-built by TFK and shipped to our base in Velsen-Noord, which is located at the North Sea Canal. Tom Nooij: ‘Our site has more than 20,000 square metres of storage space available for subsea cables – it’s the largest depot for power cables anywhere in the world. We are also experts in managing the overall logistics process for subsea cables. We use specialised machinery and ships to collect cables from factories and transport them to wind-farm projects throughout the world.’
Miles and miles
Tom, explaining the process: ‘The manufacturer produces the subsea cables, which are then installed by the installation company. The power company uses the cables, and we handle the rest.’ The company certainly has its work cut out for it with the Fryslân wind farm. By way of illustration: subsea cables have a diameter of 20 centimetres, while one metre of cable weighs more than 50 kilos. Some cables at the Fryslân wind farm are as long as 7 or 8 kilometres, and they are transported to Velsen on special barges across Dutch inland waterways. ‘Once they have arrived there, we make sure they get to the installation company in time.’
Backyard project
Tom and Gert have been working together from their various businesses for many years, and both men are excited to contribute to the construction of the Fryslân wind farm. Gert feels it’s a special experience because the wind farm is a homegrown Dutch project. Tom, adding: ‘They’re working with a Dutch installation company and a Dutch cable supplier, all companies we work closely with as well. It feels good to have them as partners in the energy transition.’
Getting everything ready
Partners TKF and WIND B.V. are no strangers to large-scale projects such as the Fryslân wind-farm project. Tom: ‘We do this every week, often working with several partners at the same time. I personally tend to think that is our strength.’ Gert agrees: ‘Even though our company is located on the other side of the country, our partnership with WIND B.V. and other companies based in the Amsterdam Metropolitan Area has been surprisingly smooth, amicable and efficient. I’m struck by how generously inclined companies based in this area are towards each other, in terms of how they work together and give each other – often literally – the space they need.’ Tom: ‘Together, we never fail to deliver for our customers, and our aim is always to exceed expectations.’
Enough energy for the future
Gert and Tom expect their role in wind-farm construction will only become more important in the future. Gert: ‘The distances from the coast keep growing and the wind farms keep increasing their capacity, which calls for both larger cables and larger quantities.’ Tom: ‘This also means it’s becoming progressively more difficult to get them to their destination on time.’ All this already requires high-level logistics management and a good bit of improvisation. ‘We manage to pull it off together every time,’ Gert tells us proudly. ‘Our work in the Amsterdam port area has given us the solid experience we need to handle the logistics challenges of other major projects, including in the North Sea. Still, we always feel the need to push ourselves to do better. We want to improve our logistics and make our partnership even more efficient, as well as enhance the safety of the work. That’s why we invest in information technology and other resources, with the objective of transporting more wind power ashore in the future.’