Damen launches new ballast water treatment solutions onto the market
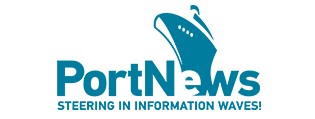
Damen has recently launched two new ballast water treatment solutions onto the market. The new products, Damen LoFlo and Damen BalCon are a response to the IMO Ballast Water Management Convention 2004, which is edging ever closer to ratification and the US Coast Guard Ballast Water Management regulations already in force, the company said in its press release.
Once the IMO convention passes into legislation, an estimated 60,000 vessels worldwide will require retrofitted treatment systems. To avoid costly vessel downtime it is imperative that installation be carried out swiftly and reliably. To meet this goal, Damen has developed standardised systems, using proven technology for a ‘one time right’ approach.
Speaking of the new containerised ballast water treatment system, BalCon, Gert Jan Oude Egberink, Manager of Ballast Water Treatment at Damen, explains: “The unique point about this is that pre-fabrication and testing can be carried out onshore, before installation. That way, when a vessel comes to the yard for repair or survey, the system will be ready to go. It’s simply a case of ‘plug and play’ – connecting the treatment system and then business as usual, with the absolute minimum of downtime for the vessel.”
BalCon covers a wide range of capacity requirements from 100m3 up to 750m3 per hour. Damen has developed the system with ballast water treatment equipment from its partner Trojan Marinex and a BioSea version is also in the pipeline. BalCon is designed to use minimal space, with all equipment contained within a single TEU.
This is especially useful when BalCon is to be installed on a container vessel, as the system is purpose-built to fit within the cargo hold. BalCon is also well-suited to tanker vessels, where the container is installed as a deckhouse. Not only does Damen offer BalCon in an optional explosion proof form for tanker usage, but there is also an option of a booster pump.
Damen LoFlo, powered by BioSea, is designed as a solution for vessels requiring a lower capacity treatment system. Currently, most offerings commence with a capacity to process 100m3 per hour, leading to an unnecessarily high energy consumption and bigger footprint. LoFlo is available with either 30m3 or 60m3 capacity, significantly reducing footprint and energy usage. The system is fitted, in a compact arrangement, to a skid for easy and efficient installation on board the vessel. It can also be installed as a modular version.
Mr Oude Egberink sums up the developments, saying, “To assist owners in meeting the ballast water management challenges, Damen offers worldwide, one stop shop BWT retrofitting. With these new products we are meeting market requirements for easy, reliable retrofitting within a very short timeframe, solving the need for ‘one time right’ installation.”
Damen Shipyards Group operates 32 shipbuilding and repair yards, employing 9,000 people worldwide. Damen has delivered more than 5,000 vessels in more than 100 countries and delivers some 160 vessels annually to customers worldwide. Based on its unique, standardised ship-design concept Damen is able to guarantee consistent quality.
Damen’s focus on standardisation, modular construction and keeping vessels in stock leads to short delivery times, low ‘total cost of ownership’, high resale values and reliable performance. Furthermore, Damen vessels are based on thorough R&D and proven technology.
Damen offers a wide range of products, including tugs, workboats, naval and patrol vessels, high speed craft, cargo vessels, dredgers, vessels for the offshore industry, ferries, pontoons and superyachts.
For nearly all vessel types Damen offers a broad range of services, including maintenance, spare parts delivery, training and the transfer of (shipbuilding) know-how. Damen also offers a variety of marine components, such as nozzles, rudders, anchors, anchor chains and steel works.
In addition to ship design and shipbuilding, Damen Shiprepair & Conversion has a worldwide network of 15 repair and conversion yards with dry docks ranging up to 420 x 80 metres. Conversion projects range from adapting vessels to today’s requirements and regulations to the complete conversion of large offshore structures. DSC completes around 1,500 repair and maintenance jobs annually.